Rise of laser processing and the need for beam shaping
In recent years we at Holo/Or see an increasing interest in laser welding and laser additive manufacturing, often using high power lasers with 100W to multi-kW power range. While theoretically higher laser power enables increased process speed, in practice there are often process physics limits to the improvement.
For additive manufacturing, this limit is the need to maintain resolution of printing, to avoid course build granularity and waviness, while for welding the limit is often caused by melt pool instability at high speed giving raise to humping and undercut.
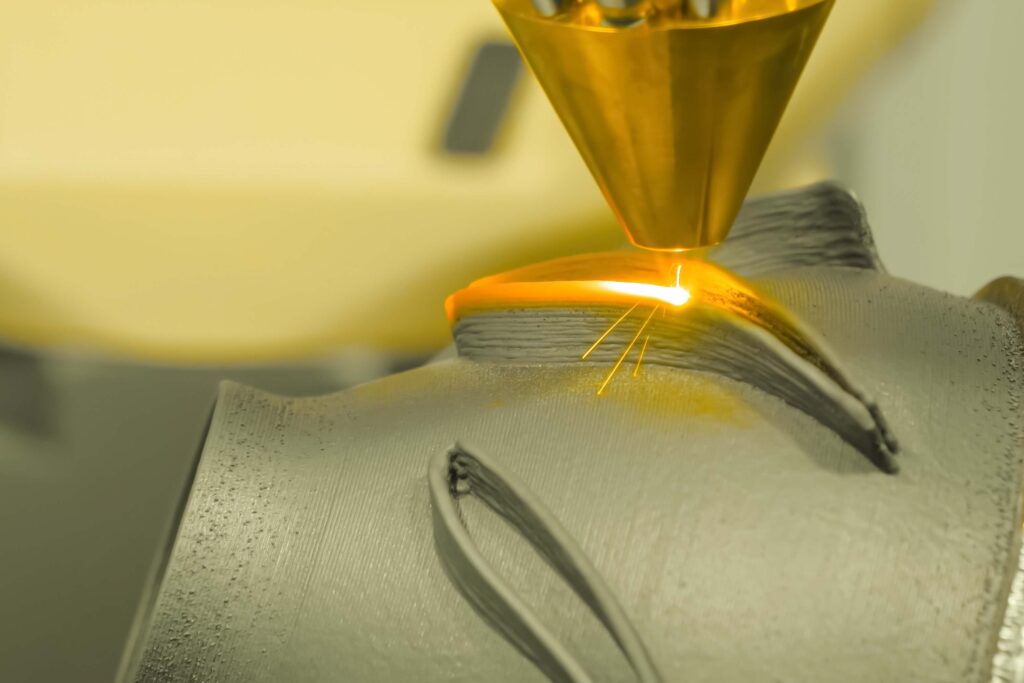
A common method of overcoming this limit is the use of a laser beam shaper to tailor the spot properties to the process. In this article, we review some considerations and show some examples of laser beam shaping in welding and additive manufacturing.
So what is Laser beam shaping?
Most high power lasers have Centro-symmetric distributions, often gaussian or semi-gaussian ones, with the power highest at the spot center and gradually decreasing toward the edges. This natural spot shape is often suboptimal in laser material processing, requiring shaping of the beam.
In broad terms, beam shaping is a process where a laser beam undergoes a re-configuration to mores process optimal distribution. This is often done through the use of a laser beam shaper, a diffractive or refractive component that manipulates the beam, typically placed before the system focus lens.
Laser beam shapers belong to several families: laser beam homogenizers are typically used to make the intensity of a beam more uniform. Laser beam splitters split the beam into an array of spots with pre-configured power ratios, while beam shapers such as top hat shapers, diffractive diffusers, spiral phase plates and diffractive axicons can modify the shape of the spot to a flat top, donut, line, or any other desired shape.
Limitations and requirements for laser beam shaping
A laser beam shaper, while a powerful and versatile tool, has certain limits that must be taken into account when considering it’s integration in a welding or additive manufacturing system. These include:
- The diffraction limit- a laser beam shaper cannot produce a shape whose size is smaller than the spot produced by the system without the beam shaper.
- Minimum beam size – small spot shapes are often desirable for achieving high resolution in laser additive manufacturing. Small laser beam shapers often require large input beam size, to achieve the required diffraction limit.
Laser Beam Shaping Applications in Additive Manufacturing
Additive Manufacturing poses unique challenges to laser beam shaping. The main issue is the need to increase the spot size as little as possible, to maintain print resolution, while at the same time shaping the beam to move energy from the center to the external diameter.
Various methods can be used for laser beam shaping that increases spot size as little as possible. A popular method is the use of small diffractive beam shaper elements, that can be tuned to provide a donut with diameter X1.5 times the gaussian spot size . These are robust, cost-effective elements with shaping functionality limited to a relatively narrow defocus range. For additive manufacturing applications where more depth of focus is needed , the use of spiral phase plates is recommended. Spiral phase plates smallest donut size is typically X2 times the gaussian spot size.
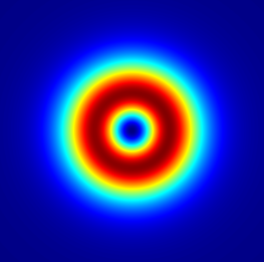
Beam Shaping in laser welding.
The requirements of typical laser welding applications are for larger spots compared to additive manufacturing, enabling more shaping flexibility. For fast welding of thin metal, of the limiting factor is the melt pool instability , thus we have developed a shaping a approach that deals with this issue , Holo/Or’s Flexishaper. This module can create a spot with a ring around it, with adjustable power ratio between ring and central spot. This allows the laser power to stabilized the melt pool while performing the main weld, improving weld speed, and can be adjusted for different material thickness or laser scan speeds.
Other types of welding, such as T weld and but-joint welding, have their own optimized laser spot distributions. These include double spot welding configurations such as those generated by our scanning HEDS , a family of 1X2 laser beam splitters where the power ratio between beams can be easily adjusted by decentering the DOE. Other useful laser beam optics for welding include tailored shape diffusers, diffractive axicon ring generators and analytic beam shapers for single mode fiber laser (typically used in micro welding).
Summary
Laser beam shaping is a highly useful technique for process optimization in laser welding and laser additive manufacturing. It allows for better melt pool stability, faster processing, and increased quality. DOEs are a common method of laser beam shaping, and their high LDT, high accuracy and flat surfaces make them easy to integrate into existing setups.
Do you have a laser welding or additive manufacturing application? do not hesitate to contact us for all your laser beam shaping needs.
TL;DR:
What is laser beam shaping?
Laser beam shaping is a technique where the distribution of the laser is changed. Typically, this is done at the focus plane of the system resulting in different spot size and energy distribution.
Why is beam shaping important for welding and additive manufacturing?
certain processes in welding are limited by melt pool instability when going to high speed. A correct spot shape mitigates this, allowing faster welding. In additive manufacturing, smoother melting is achieve with donut shapes, and by beam shaping faster processing can be achieved in the internal volume of the build, where resolution is less critical.
What are the requirements for beam shaping?
Beam shaping requires sufficient beam size and always increases the spots size compared to the un-shaped spot.