Diffractive optical lenses, more accurately known as diffractive optical elements or DOEs, are the preferred go-to beam shaping and splitting solution for many laser system integrators.
DOEs have a wide range of advantages
The basic and most distinct advantage of a diffractive optical lens is its dimensions: simply being flat, thin and easy to integrate is in many cases enough to “seal the deal”.
Take a diffractive axicon for example, as opposed to it’s refractive thick, bulky, pyramid-like counterpart. There is no doubt that the diffractive option is the easier one to use:
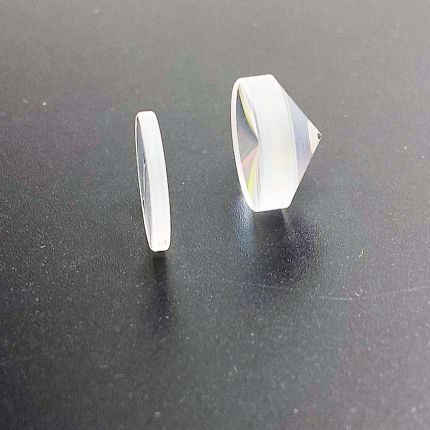
Another clear advantage of the diffractive optical lens is its extremely high accuracy and low production tolerances, due to its production process: unlike refractive optics, which are typically produced by mechanical procedures of grinding and polishing, DOEs are fabricated by lithography and etching methods similar to those used in the semiconductor industry , thus enjoy effectively absolute accuracy in feature spacings, which translates to absolute accuracy in angles.
Diffractive optical lenses also have functional advantages which can make them highly cost-effective when designing an industrial system meant to operate reliably at a high degree of repeatability.
For example, when using a diffractive beam splitter, one can achieve accurate separation distances that are a few diffraction limits. To achieve this by refractive methods, a re-imaging system is often needed, limiting the use of components such as scanners. Another alternative is active scanning over the spots array, but this requires a high-cost active component that must be integrated into the system architecture, and has inherent speed limits.
With a diffractive beam shaper, which generates a flat-top intensity distribution at any desired shape, the alternative, if any, consists of a complex optical module with multiple optical components generating inferior performance with higher tolerances at larger dimensions.
So why not always use DOEs?
As good of a solution as diffractive optical lenses may be, they are not perfect for every application. DOEs have their limitations, the first being the fact that they are phase elements meaning – if your system uses more than a single wavelength, or if you have a light source with a broad spectrum, you may need more than a single DOEs to meet your shaping needs.
Another constraint of using DOEs is that they are passive components, making the use of them a great method for repetitive processes which are typically the case with commercial applications, but are less attractive in setups where flexibility in shaping by the same source is required.
Finally, diffractive optical lenses in their most basic binary form are generally less efficient than refractive optics, which can constitute a deal breaker for extremely demanding applications. This and all the above obstacles can be overcomed by customizing the diffractive optical element design to one’s needs.
Polychromatic beam shapers, diffractive achromats and diffractive beam combiners are some examples of coping with chromatic issues. Flexishaper(™) and scanning HEDS are DOEs which provide adjustable, semi-active, shaping functions. And lastly, multilevel designs are the answer to generate high efficiency shaping.
To summarize, diffractive optical elements are one of the best beam shaping and splitting options available today. This technology is evolving with the constant developments of new and improved solutions to the requirements that arise every day, as engineers and scientists challenge the conventions and explore better, alternative, manufacturing processes that harness the power of lasers.
Holo/Or welcomes all our partners to contact and challenge us with any beam shaping need – basic or complex.
TL; DR - Q & A
What are the advantages of using diffractive optical lenses?
DOEs have a wide range of advantages over their counterpart refractive alternatives: they are flat, thin, lightweight and generally compact solutions. They also enjoy absolute angular accuracy with very little production tolerances thanks to their fabrication technique. In some cases, DOEs also present a more robust and economic solution than others.
What are the constraints of using diffractive optical elements?
DOEs are not perfect for every application. They are monochromatic, passive components, with generally less efficiency than refractive optics, which can be resolved by a multilevel design. The other mentioned constraints have several resolutions that vary by case and requirement.
When is a diffractive optical element a good solution?
There is no clear cut answer to this question, but generally, in every high-precision industrial or commercial system meant to operate reliably at a high degree of repeatability, DOEs would be the best option.