As laser beam welding continuous to expend, there is increasing need for Laser beam shaping optics to enable high throughput while maintaining welding quality. Holo/Or offer multiple beam-shaping solutions for welding, including the Flexishaper ring and spot module, C shaper and M shaper.
In the past few decades, the welding industry has been revolutionized by the introduction of laser beams to the field. The continuing increase in laser power and reduction of the cost per watt , as well as the rising availability of lower cost fiber coupled laser have driven the growth of laser welding application. As power is so readily available, it is often no longer the main bottleneck in welding laser application. Other factors such as undesired physical processes (humping, undercut) , control and synchronization and thermal constraints are now becoming the new bottleneck. One of the main tools for improving laser welding speed and quality and overcoming these bottlenecks is beam shaping. i.e creating tailored intensity distributions that are optimized for specific welding processes. . In this article we will discuss such laser beam shaping techniques and laser beam shaping optics for laser welding applications.
Methods of beam shaping for laser welding:
Given a set of parameters such as welding speed, laser power, material thickness and others, an optimal laser beam shape can be found that gives the most uniform weld without humping or ripples and achieves full welding at both top and bottom of the weld . Some of these intensity shapes may include:
- M – shape:
Since a gaussian beam distribution has a maximal power at its center and a decrease at its edges, when it is used for conduction welding, the melt pool is unevenly heated, resulting in impurities and defects such as humping. .
An M shape or ring-like power distribution is desirable for laser conduction welding applications as it creates a more uniform thermal distribution in the melt pool, as heat diffuses from the ring both inwards and outward.
- C-shape:
A C-shape laser beam allows bubbles and other weld defects to be released from the melt pool in an ordered manner through the opening of the C-shape, as opposed to closed shapes which distribute energy in all directions evenly, trapping the bubbles and defect in the cooling melt pool as the laser beam moves past it. Thus, C shapers enable improved weld strength, but require orientation vs the weld direction, thus are mostly suitable for line welding or lower speed welding. Ring-spot combination (Flexi-shaper):
When welding with a gaussian shaped beam, undesired phenomena often occurs when attempting high welding speeds, as the molten metal cannot wet the cooler surface left in the wake of the passing beam. This causes the metal to bead as it cools, creating a hump-like seam surface, thus it is called humping. In order to fix these issues a beam made of a combination of a ring and central spot can be applied to pre and post heat the surface prior to the welding, resulting in a much better wetting and elimination of humping . This can be done by the flexi-shaper module, which provides a solution for laser beam shaping applications requiring a combination of a ring and a spot. The flexi-shaper enables tuning of the distribution of energy between the spot and the ring in order to achieve the optimal laser beam shape for each process. The tuning of energy can be seen in figure 1.
In a process test done by Blackbird Robotersysteme GmbH, the flexi-shaper was used and thanks to the ring-spot distribution a 40% increase in welding speeds were achieved compared to the maximum possible with a gaussian laser beam shape. Results of using the flexi-shaper laser beam shaper solution can be seen in figures 2,3.

Another beam shaping method can be usable for laser welding process monitoring and control. For multi kw lasers used in welding, It is often difficult to sample both main beam power and get a beam profile at the same time, as cameras often have much higher sensitivity (and lower LDT) compared to high-power power meters. This issue can be solved by using a single diffractive sampler. A diffractive laser beam sampler is a Diffractive Optical Element (DOE) designed to split a sub-beam identical to the main beam , with pre-determined small fraction of power, for example 0.2% . The main beam power can be sampled directly from the sample forward order with a power meter, while the reflected sampled order (which is attenuated by another factor of ~100 compared to the forward order) can be used with a camera to monitor the beam profile. This enables real time control of both power stability and beam profile.
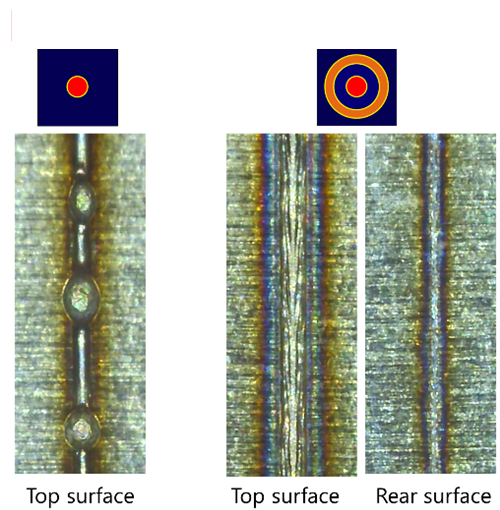
TL; DR – Q&A SUMMARY
Why is laser beam shaping required for laser welding and laser beam shaping applications?
When it comes to laser beam welding, numerous undesired phenomena can occur when attempting higher welding speeds. When a custom shaped laser beam is utilized, these phenomena can occur in much higher speeds then with a gaussian laser beam and a much more uniform weld can be achieved.
What shapes are normally applied to laser beams for laser welding?
Most often shapes such as M-shape, C-shape or a ring-spot combination are used for laser welding.
What other functions can laser beam shaping achieve?
Laser beam shaping can be used for laser beam samplers and any other laser beam shaping application which requires a
Top Hat power distribution or any other custom laser beam power distribution.