A beam shaper top hat is a diffractive optical element which alters the phase of an incoming Gaussian beam into a flat top shaped energy distribution. This article will discuss the beam shaper top hat’s qualities and when it is advised to use it.
Introduction to beam shaping optics
Nowadays, the advancements in laser manufacturing and power availability enable improvements in many laser based applications by shaping the laser beam into various energy distributions that are tailored for specific treatments and processes, allowing higher throughput and quality in laser processing .
When referring to beam shaping optics, there are several different methods available in the market starting with a simple coarse glass which diffuses the light that goes through it to produce a homogenized beam to complex optical modules composed of multiple lenses and other optical elements.
This article will focus on one laser beam shaping method which is compact, cost effective, and most importantly – provides the most accurate beam shaping results – the diffractive beam shaper.
Generating flat top beam profile with a diffractive beam shaper
A diffractive beam shaper is an analytical optical component, i.e, it performs a well defined optical function whose output is a known continuous phase profile, without phase randomization. It is a flat, window-like element, with a unique computer optimized pattern etched into its surface in micron scale steps. The etched pattern, when illuminated, creates phase delays to portions of the light which goes through the element. When designed correctly to a specific input beam, these phase delays can be controlled to ultimately generate an image at the output with almost any desired shape and size characteristics. Moreover, the generated beam shaper light has a very homogeneous and uniform energy distribution within the shape, with sharp edges between the area containing the energy and the area with no energy.
This type of energy distribution, when focused, can provide a competitive advantage to many laser system integrators, specifically in material processing applications such as laser micro machining, accurate scribing of solar panels, etc.
Why is beam shaping required for the laser beam?
Although power is becoming more and more available, it is still one of the most expensive ingredients of the laser based system through the entire equipment lifetime from design, through engineering and operation stage. Therefore, utilizing the available power in the most process optimized manner is advised. That is where the diffractive flat top beam shaper comes in.
The shaped laser beam is, in most cases, custom designed for a specific system and process parameters. It is typically defined in a way which will determine the output to be flat just slightly above the required process threshold to avoid any unnecessary energy waste. The output beam shape and size will also be adjusted to the required process parameters to enable maximum processing efficiency and by that – increase the equipment threshold when compared to using a non-shaped beam (a Gaussialn beam).
In addition, thanks to the zero angular tolerance of the diffractive optical element manufacturing process, integrating a beam shaper top hat into a system guarantees process repeatability between multiple similarly designed systems, with no dependency of the processed area on the laser pulse energy, unlike the case with a typical Gaussian beam.
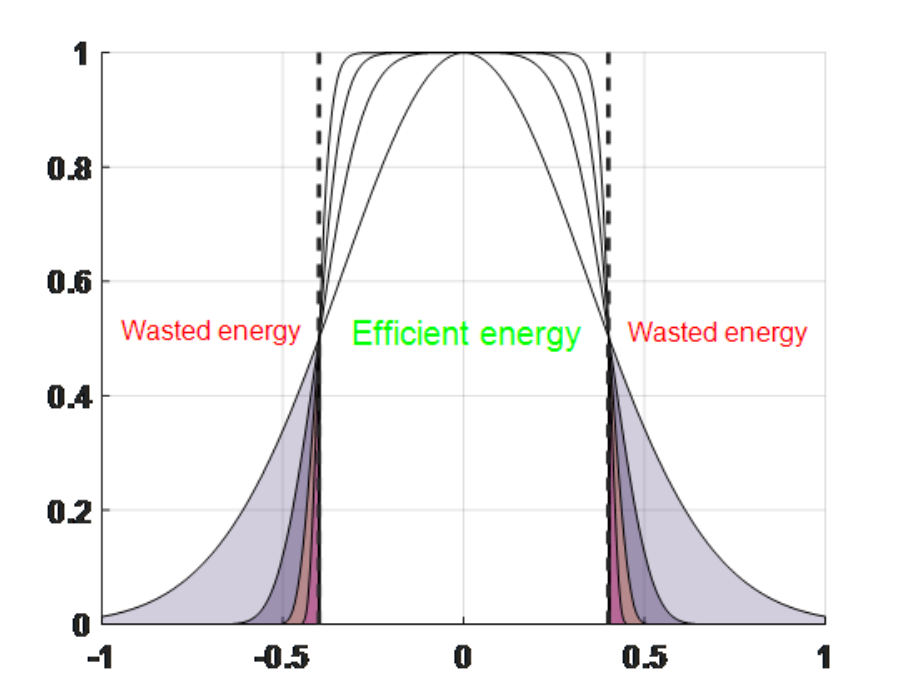
When is using a beam shaper laser advised?
Not every system can use a beam shaper top hat, and not all should.
The beam shaper top hat optical component, due to its unique qualities, is normally integrated into high value systems which require a very accurate treatment, especially in cases where multiple systems need to operate in the same manner. A common use for them is in systems where if some of the energy was allowed outside the desired treated area, it would introduce damage to the processed workpiece.
There are some hard requirements for using a beam shaper top hat – the input must be a highly coherent single mode beam with M^2 value < 1.5, and there is an additional condition on the ratio between beam diameter and the optics clear aperture.
In other cases, where shaping is desired but the input beam is a multimode beam, other beam shapers such as a diffractive diffuser or a broadband diffuser can be used. Both options provide excellent shaping qualities and increased system throughput, and are typically used where a large area needs to be treated and not a focused one.
TL; DR - Q&A
What is beam shaping?
Beam shaping, in its wide sense, refers to generating a different output image of a laser beam that of the input beam.
How does a beam shaper work?
There are different methods and types of laser beam shapers, each providing different qualities and is appropriate for use with different systems. These include the beam shaper top hat, diffractive diffuser, broadband diffuser and others.
When is using a beam shaper top hat advised?
A beam shaper top hat is advised for use in high-valued, high-powered laser systems with single mode lasers, where optimizing pulse power usage is an advantage and where process accuracy on the treated area is crucial.